第1章 実例で探る改善策
【2】B精工・不況下で最高益の更新を続ける
5年前には営業利益の黒字安定化が課題だったB精工が、リーマンショック後の大不況下のH22年決算期に全社員に特別賞与を支払い、尚且つ実質8%を超える営業利益率を達成しました。そして今、“生産性倍増”へ向けて次の3ヶ年計画のスタートを切っています。改革を通じて大きく成長した社員一人ひとりの“高い意識”が会社の成長を支え、社長を中心に大きな目標に挑戦し、改革を通じて更に社員が成長するというよい循環が生まれています。
1、意識改革は4S(整理、整頓、清潔、清掃)から
4Sは改革・改善の基本です。会社の良し悪しは「4Sと出勤率でみる」とは多くの企業を買収して成功してこられた日本電産社長の言葉です。自分の身の回りを整理整頓できなくてよい仕事ができるはずがないということです。
5年前のB精工も取引先に「汚い」といわれその汚名を返上することが差し当たっての課題でした。その工場が僅か1年で大変身したのです。そして今では日本を代表する世界的な企業や、省庁幹部の行政研修の見学コースになるなど、外部の評価が日に日に高まっています。
僅か1年で職場が大変身したのはナゼ?
要点は
・社員を教育して
・社員の力で
・社員が協力し合って自主的に改善する「仕組み」をつくること
そのために私が行ったことは次の3点でした。
(1)4Sの進め方の講義
(2)PDCAをまわすアクションプランの作成指導
(3)4Sのゴールのイメージを写真で見せる
2、“高い目標”が会社を変える
抵抗にあった“生産性30%UP”
支援が始まった当初、製造部に生産性“30%UP"の目標設定を提案しました。当時月産500万個だったのを1年後に月産650万個にしようというものでした。しかしそれが「それは不可能です」との製造部の抵抗にあいました。
設定したいのは、初めからできるとわかっているレベルの目標ではありません。簡単には達成できそうにない高い目標です。私は支援の経験からB精工でも、必ず30%程度の改善はやってくれるものと確信していました。
期間は1年あります。その間目標を追い続ければ打開策は必ず見つかるものなのです。製造部の回答は「5%なら出来ます」というものでした。改革・改善に抵抗はつきものです。
又、多くの企業で5%~10%レベルの目標設定が通例になっているのも事実ではないでしょうか。結局、目標を「10%以上」とし「以上」を強調して活動はスタートしました。
僅か3ヶ月後に月産850万個、前年比70%UPを達成しました(図)。
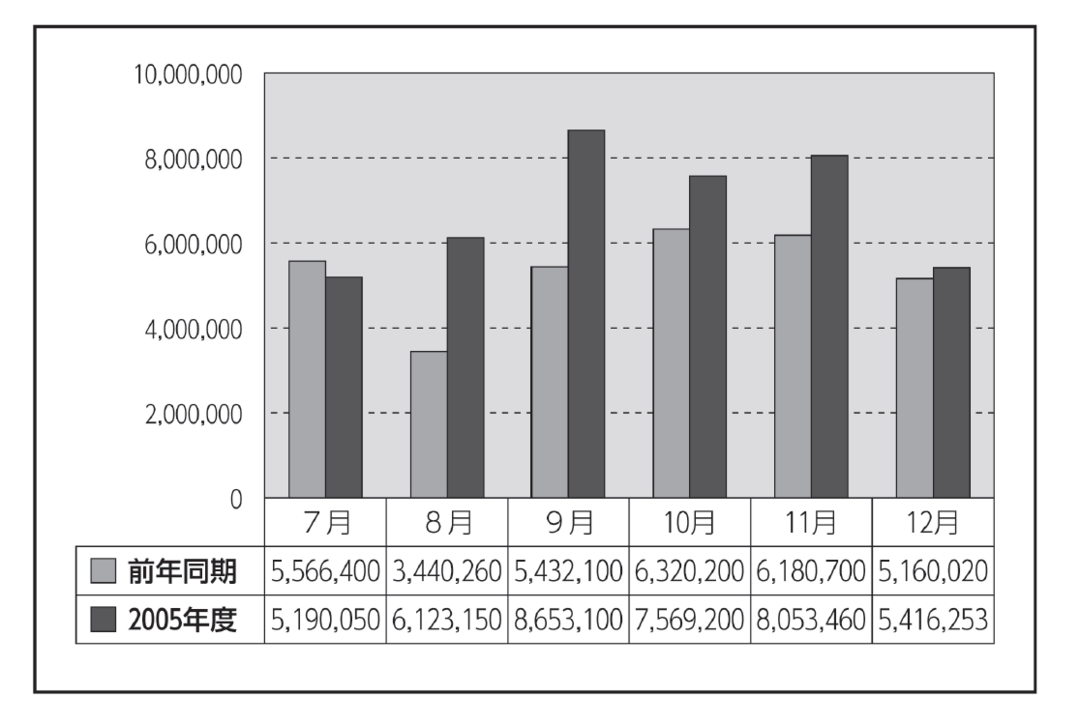
私が対策の立案についていつも強調していることは、社員の「ガンバリ」でやるのではなく、機械・設備や治工具の改善、作業方法など、仕組みの改善によって目標を追求することです。改善の方法はいくらでもあります。
ですから「知恵と工夫」でラクして生産性を上げる発想が重要です。そして、その仕組みが変われば、それが会社のノウハウや体質となって確実に蓄積されていきます。
そのような思いをこめてB社の活動は始まりました。着々と改善が進み、少しずつ成果も上がっていましたが、受注が順調に伸びたこととあいまって、僅か活動3ヶ月目に月産“850万個”を達成しました。単月では初期値の実に70%UP、いうまでもなく月産新記録でした。
何が効果的だったか責任者に聞くと、次の2点を指示したとのことでした。
・退社後の無人運転を思い切ってかける
・壊れてもいいから、機械の回転数を思い切って上げる
製造部が単なる「ガンバリ」ではなく、又「熟練と経験」に待つのでもなく、「機械設備の使い方の工夫」によって生産性を大きく向上できることに目覚めた瞬間だったと私は思っています。事実これを契機として製造部門の改革は一気に進みました。
●教訓
1、意識改革は「4S」から
2、高い目標が会社を変える
3、「ガンバリ」より知恵と工夫で「仕組みの改善」